Audi, Turning Automotive Emissions into Valuable Resources
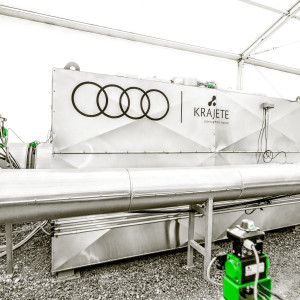
Krajete supported German car giant Audi with emissions treatment technology over thirteen years When Audi first engaged Krajete GmbH to produce synthetic methane using microbes, Game of Thrones was premiering on television screens and the Fukushima disaster threatened Japan's nuclear safety. Thirteen years later, the partnership has evolved to yield technologies to capture carbon dioxide (CO2), nitrogen oxides (NOx) and other harmful emissions from cars, stationary engines and, even, whole cities.
But how did a small biotechnology and emissions valorisation start-up end up in more than a decade of collaboration with a multinational manufacturer? As the 2010s began, viable electric vehicles (EVs) were still an ambition to be realised. The department for sustainable development at German car manufacturer Audi explored e-fuels as potential replacements for fossil fuels.
It quickly identified a need for virtually endless quantities of CO2, for conversion to methane, to make them commercially viable. The Sabatier process is a conventional way of producing methane using CO2, but requires 300-400?C and 20-30 bar for worthwhile yields. When Audi engineers came across a poster in 2012 displaying biological methane preparation using archaea, sponsored and mentored by Dr Alexander Krajete, they enquired immediately about its scalability.
The mild, gentle nature of biological methanation attracted the sustainable development personnel. Chemical methods are usually involve harsher and more demanding conditions than biological ones, which tend to operate in natural environmental parameters. Over the following two years, Audi contracted Dr Krajete to develop this microbial methane production method.
They launched a small visibility study and generated recognition among the scientific community, but the lack of end use business case and difficulty obtaining sufficient CO2 led the manufacturer deciding not to invest in an upscaling second stage plant. This didn't spell the end for the collaboration, however. Progress towards capturing large volumes of CO2 intended for e-fuel production, plus Audi's admiration for Dr Krajete's ingenuity, led to a new project in a different field.
Solving direct air capture issues
During his CO2 supply development work, Dr Krajete tested different materials to host active sites to which gas particles could bind in macro-, micro- and mesopores. One of these was a synthetic zeolite structure that he found, incredibly, was capable of adsorbing up to ten per cent w/w of CO2, e.g. ten grams adsorbs one gram of CO2. The advantage of the physisorption approach is its regenerative nature.
Rather than traditional sacrificial processes that irreversibly convert emissions, like mineral carbonation, physisorption uses very weak forces to bind gas particles. This means they can be recovered easily and used as raw materials in industrial processes or sold to third parties. The inorganic zeolite framework can extract more than 99 per cent of CO2 across a wide range of concentrations, from micrograms to parts per million and higher.
When the European Union Emissions Trading System (EU ETS) set heavy restrictions on CO2 emissions in 2013, later postponed until 2018, this technology appeared ready to shake industry sectors across the continent. Audi's sustainable development was especially interested in the potential for this gas capture. Although the biomethanation pre-project was terminated, they requested further funding to allow Dr Krajete time to show the efficacy of direct air capture (DAC) using this zeolite filter.
Within weeks, he demonstrated that it both worked and was scalable to greater volumes. "The material's hydrophobicity is crucial to its suitability," explained Dr Hagen Seifert, head of sustainable product development at Audi. "Having to pre-warm and dry the air to remove moisture before treating it at the filter would render this technology unfeasible, but zeolite's selectivity matches the intended process." "When targeting NOx, atmospheric moisture, SOx and CO2 are removed in tandem," expanded Dr Krajete. "I was not aware initially that the material would co-adsorb moisture, but the NOx:H2O adsorption ratio is around 4:1.
"However, this water capture is advantageous. When desorbed, the water and nitrogen dioxide form nitric acid (HNO3). This is an extremely useful product for industrial processes such as manufacturing fertilisers, dyes and pharmaceutical products.
Without the captured moisture, process operators would have to source and add water separately." Open air quality treatment
At this stage, Dr Seifert identified another use case for Krajete's breakthrough. Nitrogen oxide (NOx) pollution in German cities was gaining a lot of attention, created by all combustion engines from road vehicles to factory exhausts.
"We realised that this efficient and versatile gas capture technology would have numerous applications," recounted Dr Seifert. "Around 2015, there was lots of conversation about metropolitan air quality, in the streets, in the car and train tunnels. Krajete's development could help in all these areas." This remains an area of concern in the present day.
EU Directive 2024/2881 on ambient air quality and cleaner air for Europe sets a 40 ug m-3 limit for NOx air concentration by December 2026. This will fall to 20 ug m-3 in 2030, highlighting the risk to human health. Chemically, NOx behaves similarly to CO2 so Dr Krajete adapted his design to enable near-100 per cent capture of NOx. The first major step in demonstrating the system's effectiveness was to conduct a long-term test case.
Audi installed a stationary NOx DAC unit in the centre of Heilbronn, Germany, to see its progress over 18 months. Although the Heilbronn project yielded encouraging results, Audi chose not to pursue open air DAC due to the inefficiency -- NOx makes up less than 1x10-4 per cent of the air around us, between 10-100 parts per billion. Indeed, open air NOx concentration is much less than between 10-1000 parts per million found in emissions from industrial centres like steel or cement manufacturing facilities.
For the second time, however, Dr Krajete's skillset and global pressures meant that the partnership continued. NOX capture and automotive engineering
While the original intention was not to implement Krajete's emissions adsorption filter into vehicles, the partners agreed that this was worth exploring with the technology they had developed. They focused on two directions of development.
The first and initial prompt was to deal with vehicle 'cold start' emissions. The catalyst, filters and oxidisers that manage vehicle emissions do not operate until it is up to normal running temperature. This means that, in addition to greenhouse gases (GHGs), the first moments of combustion engine operation release a cocktail of NOx, SOx, carbon monoxide (CO) and volatile organic compounds (VOC).
Krajete's filter technology could even be a solution for capturing these kind of harmful emissions from the exhaust pipe. Immediately, Audi issued an immense challenge to Krajete. Its CEO and principal scientist would have to downsize his technology from hundreds of litres to just one or two.
There was no chance of fundamentally altering Audi's car designs to make more space for gas storage, so Dr Krajete explored the feasibility of small-scale units. The longevity and ownership cost of this feature were two further concerns that Krajete had to account for at the design phase. NOx is a poisonous gas mixture in high concentrations.
There was no appetite for storing toxic gases that would have to be carefully captured at yearly servicing appointments, nor for the infrastructure and education they would require. Emissions physisorption is still a new groundbreaking technology for the automotive industry, especially in the context of the EU7 regulation. The recent trend towards internal combustion engine (ICE) -driven range extender (REx) cars will help to commercialise this solution.
Once again, Audi and Krajete had developed sophisticated tools to combat emissions to medium readiness: not yet market ready, but clearly effective and mature. So what has this ongoing partnership produced? Perhaps more importantly, what lessons can the sustainability and manufacturing industries take from it?
Lessons from a decade of collaboration
Both Krajete and Audi have taken these technologies forward to tackle emerging problems. On Audi's side, it has constructed 1,000 tonne p.a. DAC facilities to collect CO2, the cheapest method of doing so.
Dr Seifert hopes that these kind of carbon capture technologies will soon make it possible to quantify exactly how much CO2 is being captured at exhaust outlets. This will enable companies to publish these numbers and market the environmental impact of its products transparently. Additionally, the automotive industry will continue developing ways to adapt the emissions filter to deal with in-vehicle gases, e.g. inside the passenger compartment.
Until automotive combustion engines are completely replaced by batteries, the unseen danger of ICE emissions persists. "The biggest lesson for me has been what a one-person operation can achieve," admitted Dr Seifert. "Audi is well-organised and effective, but Dr Krajete worked very quickly indeed. We presented him with our ideas and he solved the problems, providing great results in a short time.
I was very impressed with his ability and creativity. "I would like to be able to go further and push sustainable development to the front of the agenda," Dr Seifert concluded. "However, we learned over the last decade, and more, that the political framework does not yet exist to bring several industry sectors together with a solution." For Krajete, the work with Audi has been a launchpad.
Several applications of regenerative emissions capture have developed as a result of the media attention generated by its collaboration with the German manufacturer. One project with a large Australian mining company has recently begun as a direct result of work done with Audi. "In the end, the intense effort that went into miniaturising our NOx filters resulted in huge efficiency gains," explained Dr Krajete. "The requirements that Audi gave to me demanded ingenuity and forced me to refine my approach."
The two companies continue to work together to bring emissions capture and valorisation solutions to market for industrial sectors that still rely on combustion engines.
Although political and financial barriers exist to implementing Krajete's physisorption technology universally, tightening emissions and air quality regulations like the incoming Euro 7 standard will incentivise action.
Learn more about Krajete's three-step NOx removal solution and find out how your business could be the next to turn waste emissions into valuable resources.
Transport & Logistics - Driving The Industry Forward