EASA Certifies Safran’s First Electric Motor
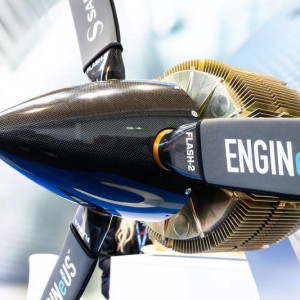
PARIS--The European Union Aviation Safety Agency (EASA) has granted a type certificate to Safran Electrical & Power for the 125 kW ENGINeUS 100B1, making it the first electric motor approved under the CS-23 standard. The approval paves the way for more powerful motors that may equip hybrid-electric regional aircraft. Moreover, Safran is preparing to use derived hybrid-electric technologies on the RISE demonstration program for a more efficient engine on narrowbody aircraft.
Safran's new motor inaugurates a new certification regulation. The Pipistrel Velis Electro two-seater was previously certified with a house-designed electric propulsion system. EASA approved the aircraft and its motor under the light sport aircraft category.
The ENGINeUS is three levels higher in terms of certification requirements, Regis Rossotto, EASA's product certification manager for the engine, said on the sidelines of a Feb.
3 press briefing. "With Safran, we did in-depth failure analysis," he explained. "Endurance trials and environmental testing, which include extreme temperature, altitude, electromagnetic interference and icing conditions, were comparable to what we require from a helicopter turbine engine." EASA's Special Condition E-19 covers all the new aspects electric motors bring. "The high-level regulation is adaptable, and the technical content is relatively light," Herdrice Hereson, EASA's section manager for general aviation and VTOL propulsion and powerplant systems. "We put the emphasis on the means of compliance." Among the tests the ENGINeUS 100B1 underwent, fire prevention involved electric arcing, to show the motor remains safe in extreme short-circuit conditions, Rachel Daeschler, EASA's certification director, said.
The motor's certification campaign involved 1,500 hrs. on testbeds and more than 100 flight hours on an aircraft, Safran added EASA has gained experience in technical conditions and compliance methods. "We will be able to reuse our learnings with other motors," Daeschler said. Other applicants for the certification of an electric motor include eVTOL developers Lilium and Volocopter, and an unspecified European engine specialist, Hereson said.
In regional aviation, the CS-23 standard limits the use of the new motor to 9-19 seat aircraft. Higher seat capacities would need motors certified under the more demanding CS-25. Meanwhile, EASA and the U.S.
FAA are cooperating for future harmonization. Safran has applied for certification with the FAA, but the process is less advanced, Bruno Bellanger, CEO of Safran Electrical & Power, said. ZeroAvia on Feb.
3 announced that it reached consensus on the certification basis relating to its 600kW electric propulsion system with the FAA. The ENGINeUS features integrated power and control electronics, meaning the airframer can keep wiring more straightforward, Bellanger said. Air cooling was also chosen for simplicity, as no oil system is required, he added.
The power-to-weight ratio stands at 5 kW/kg. Safran's production plans involve two semi-automated factories, one in Pitstone, UK (for rotors and stators) and one in Niort, France (for power electronics and final assembly). The company is planning on a capacity of 1,000 motors per year.
That output may be reached before the end of the decade, notably thanks to multi-motor aircraft configurations, Bellanger said. Among the customers, Toulouse-based Aura Aero flew its electric two-seater, the Integral E, for the first time in December 2024. The airframer is developing the ERA hybrid-electric 19-seater, for which it is counting on distributed propulsion and more powerful Safran motors.
Others include Bye Aerospace, CAE, Diamond Aircraft, Electra, TCab Tech and VoltAero. Safran is betting on in-service experience with small motors to feed into the design and certification of future, larger motors. With the ENGINeUS XL, it is aiming at powers in the 500 kW-1 MW range and has already demonstrated 730 kW, Bellanger said.
While it may be used directly as a propulsive motor, the XL may also be part of a hybrid-electric layout on a turbofan or open fan, as on the RISE demonstrator. On the RISE, the two shafts will share power in transient regimes. The architecture may help keep the engine's power to the minimum specification, as opposed to oversizing the engine to cope with marginal phases of working.
The system will rely on an ENGINeUS XL on the high-pressure shaft and a 300 kWGENeUS motor-generator, Bellanger said.