Inside the Factory: We Visited the New Electric Motor Assembly Plant of Yamaha in France
DirectIndustry had the opportunity to attend the inauguration and then visit the new electric bicycle motor assembly plant of the Yamaha Motor Group in France[1] (formerly MBK Industries). This plant, the only one in Europe, is a carbon copy of Yamaha Motor[2]'s Japanese factories. Local officials, top executives, and managers directly from the Yamaha Motor headquarters in Japan gathered last week in Saint-Quentin in the Hauts de France, a 2-hour drive from Paris, to inaugurate the new assembly plant for electric bicycle motors of the new Yamaha Motor Manufacturing Europe group.
Production started just a few weeks ago to produce around 400 electric motors per day for electric bicycle manufacturers. DirectIndustry had the opportunity to attend this inauguration and learn more about the chosen industrial model on-site, the production techniques involved, and the future envisioned for the site.
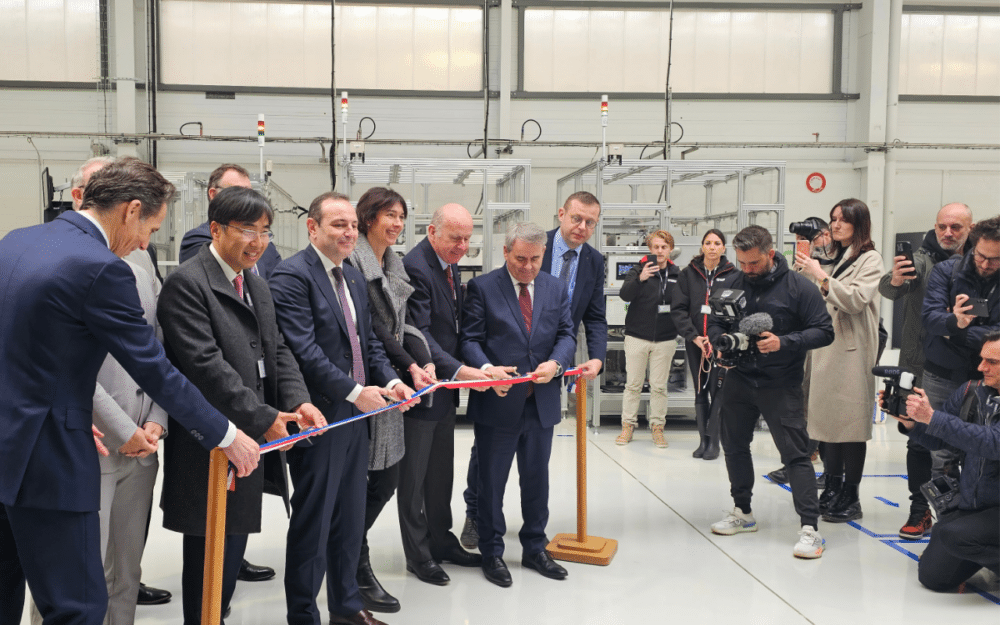
Yamaha and Electric Bicycles
Yamaha specializes in manufacturing motorcycles ranging from 125 to 700 cubic centimeters and scooters ranging from 125 to 300 cubic centimeters.
In 2023, the company produced 82,000 motorcycles and scooters. Yamaha also pioneered the first mass-produced electrically assisted bicycle over thirty years ago. Since then, the group has been supplying bicycle manufacturers in Europe, which has become the world's leading market, with kits including motors, batteries, display screens, and dedicated chargers.
In 2013, Yamaha launched its range of electric motors for bicycles, the PW Series. According to Clement Villet, from Yamaha's executive committee, the group produced over eight million motors worldwide.
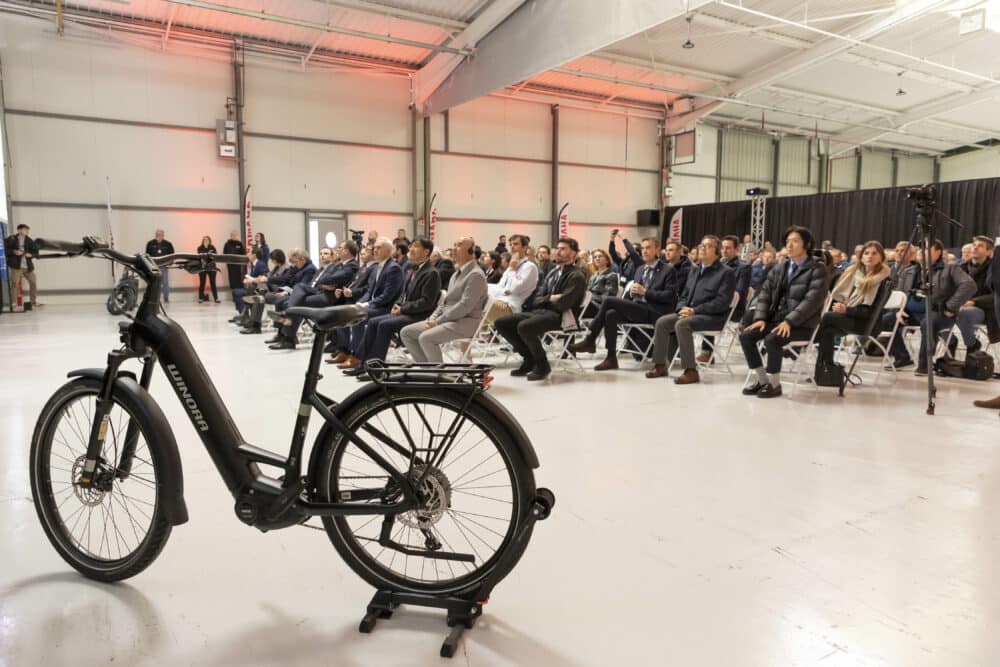
From Motobecane to Yamaha Motor Manufacturing Europe
The company Motobecane was created in 1923 in Paris. The company relocated to Saint-Quentin in 1951.
In 1984, the company changed its name to MBK Industries, and in 1986, the Yamaha Group became its principal shareholder and eventually became the sole shareholder in the early 2000s. In January of this year, the company MBK changed its name to Yamaha Motor Manufacturing Europe, fully integrated into Yamaha Motor Europe. The turnover in 2023 was 418 million euros.
639 people are permanently employed at the Saint-Quentin site. Since then, the company has begun the rollout of Yamaha electric bicycles on a new assembly line.
15,000 bicycles have been prepared and delivered to the end customer. Last March, the group opened a new assembly line for electric bicycle motors in Saint-Quentin.
This is where the Yamaha PWS2 motor will be assembled. This is the only Yamaha factory for electric bicycle motor assembly in Europe and the second in the world after Japan. The goal is to produce 400 motors per day for electric bicycle manufacturers.
According to Patrice Maciejewski, President of Yamaha Motor Manufacturing Europe, "45,000 motors will be manufactured this year, and we hope to reach our full capacity of 300,000 motors within the next three years."
The Electric Bicycle Market
This electric motor production project represents a EUR4 million investment for the Yamaha Group. The group's Japanese headquarters decided to entrust Yamaha Motor Europe with the responsibility for this activity because Europe has become the world's leading market for electrically assisted bicycles.
It accounts for three-quarters of the current global demand.
80% of bicycles sold in Europe are now assembled within European territory. Twenty million bicycles are sold there each year, among which the share of electric bicycles has continued to grow. It represents more than a quarter of sales in 2022, or approximately five million units.
Clement Villet predicts: "This ratio will continue to increase, suggesting that the share of electrically assisted bicycles should reach 50% of the total market by 2030." For Patrice, the choice to produce these motors in France, close to the demand, has several advantages:
"Notably a shortened and therefore more virtuous logistics chain. We can use our Yamaha manufacturing capabilities as a competitive and sustainable advantage to meet our customers' demand for quickly available carbon-neutral products produced in Europe. This allows us to be much more responsive to changes in market demand."
One of Yamaha Motor's main customers, electric bicycle manufacturer Accell Group[3], was present at the factory's inauguration. For Mr. Tjeerd Jegen, CEO,
"Localizing production here in France and the drive units that will be assembled here are being used in the most important brands of our company, Haibike and Winora both produced and assembled in Germany and then Batavus in Holland. And for our group Accell, it's really important to see our suppliers localizing their production in Europe because it brings more resilience to our supply chain and also helps to meet our ESG targets. And this also helps us to serve our customers in a much better way and bring products much quicker to the markets where we operate."
The e-drive Workshop

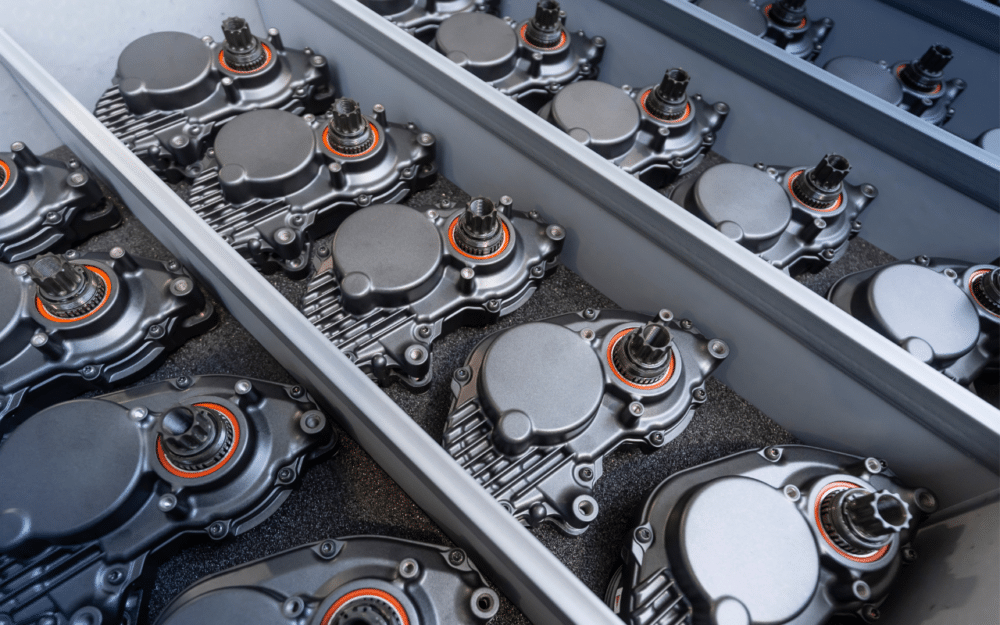
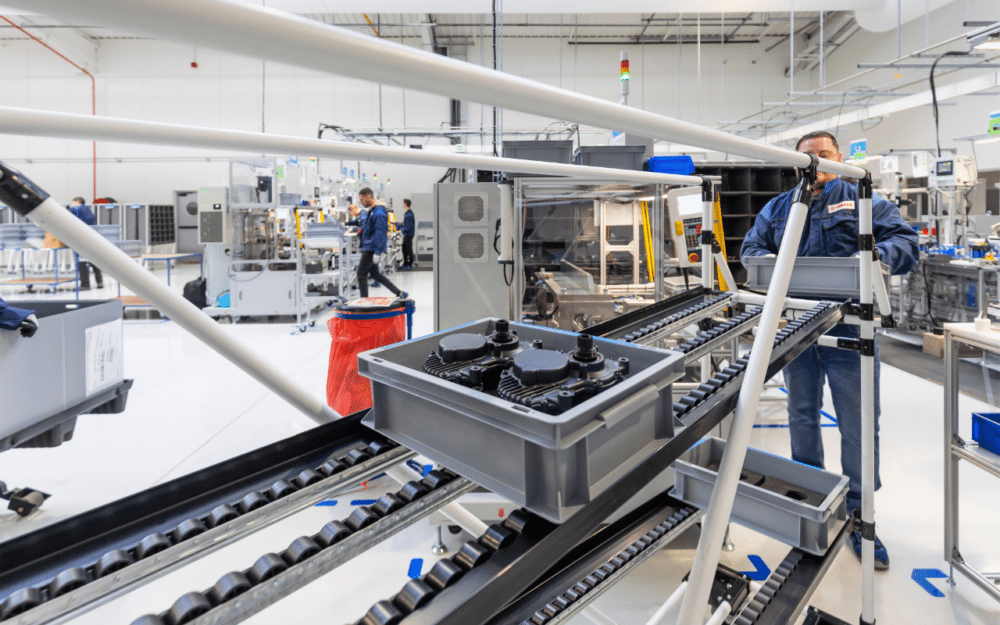
We had the opportunity to visit the assembly line called e-drive.
In this antistatic room, also known as the cleanroom, we had to wear antistatic shoes. Currently, about twenty people work there in a single shift, assembling 400 motors each day. Each motor contains around sixty parts.
The total weight of the motor is 2,850 kg. It has a power of 250 watts with a torque of 75 Newton meters. The line is divided into three parts: a preparation/logistics part, an assembly part, and a testing part.
The first two parts are mainly manual, as explained by Fortunato Campisano, from Yamaha Motor's management committee: "In the preparation part, there are presses for fitting components, but to operate them, manual actions are required. We place the components and fit them together.
Then, we assemble the different parts of the motor on the line. The motor is assembled step by step by the operators. There are seven assembly phases.
These are very meticulous operations. For example, here we have an electrical harness that needs to be connected to the intelligent part of the motor. All these small cables must be threaded by hand by the operators.
This is an operation that cannot be automated today." Operators handle tightening tools and screwdrivers. There are no intelligent systems such as AR (Augmented Reality), for example, to assist the operator.
However, when the operator takes a piece from a bin, passing the hand through the bin triggers a sensor that automatically records the action in the system and the history. Tasks are mainly manual, but there are still some automated tasks. Among the automated tasks is the application of silicone between the two parts of the motor.
Similarly, a camera measures and controls the application of silicone and the amount of grease applied to the gears. At each step, the operator must ensure quality. After the motor is assembled, it goes through two control phases before dispatch to the customer.
First, there is an automatic sealing control on a specific bench. The idea is to immerse the motor in a bath. Following this initial check, the motor proceeds to an inspection bench where it undergoes more rigorous tests.
"We recheck what has been assembled, send signals, and perform tilt tests, simulate the use of the motor on the road, on different terrains, etc. And we verify if all the angles correspond to the software programming." The line is modular and can accommodate the assembly of other types of motors, as explained by Herve Daty, Workshop Manager:
"It is sufficient to change the pallets on the assemblies. The series change can be done very quickly."
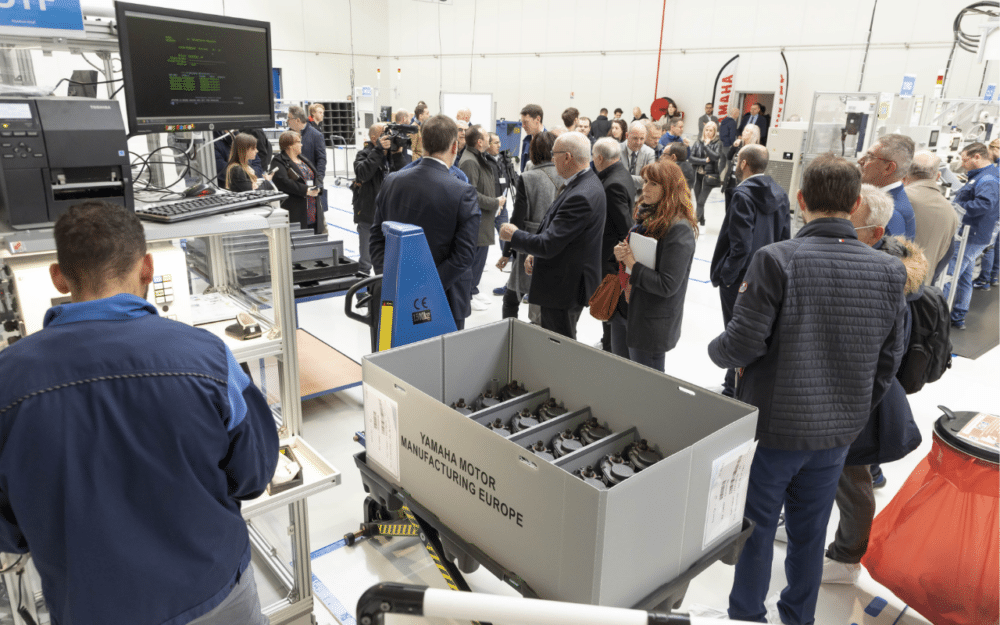
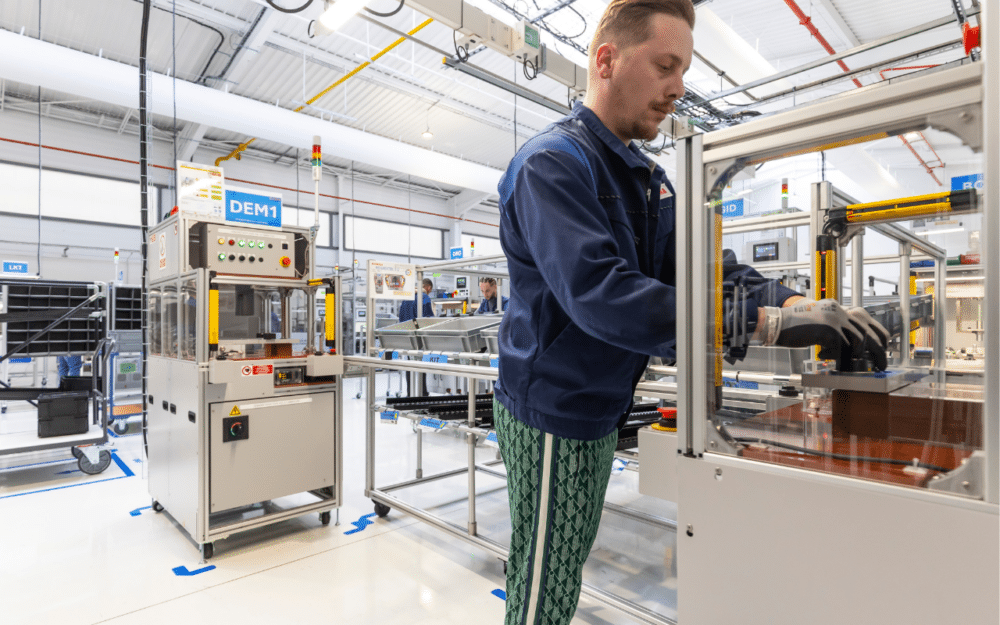
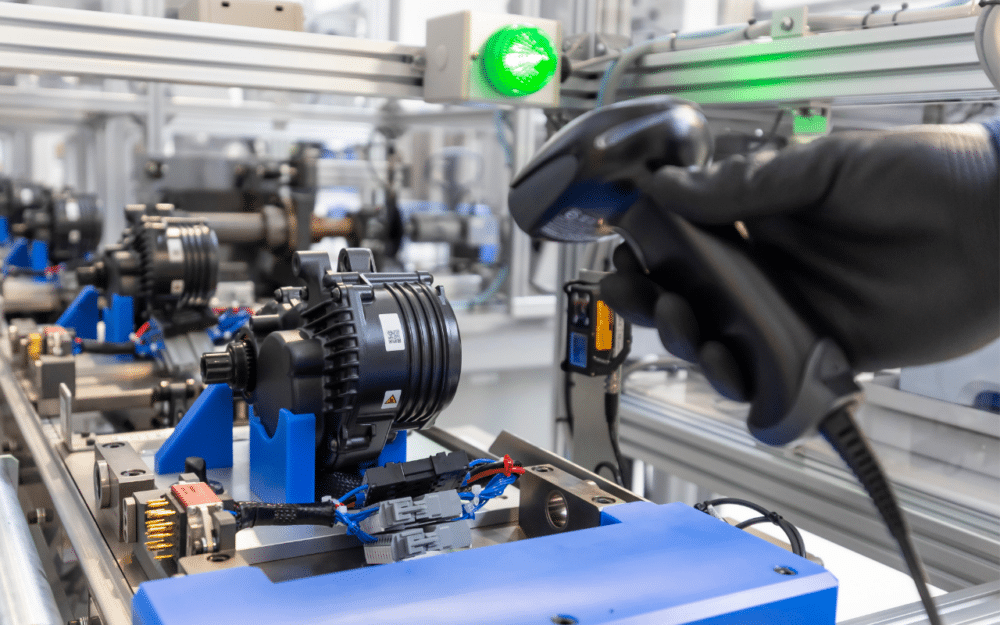
Copied from Japan
Until now, these same motors were manufactured in Japan.[4] But the particularity of the French factory is to be a carbon copy of the Japanese factories, emphasizes Fortunato: "We duplicated the Japanese methodology.
We did a copy-paste of the process that existed in Japan. Engineers from Japan came to install it. Each operator was trained for their position in the Japanese production manner by management trained in Japan, and also with Japanese personnel on-site."
The equipment, like the inspection bench, is of Japanese brand. We could thus see Yaskawa motors. The primary parts also come from Japan.
For Herve Daty, Workshop Manager: "All product evolution, modifications, and improvements are transferred from Japan and revised here. We must always be compliant and be similar to what is manufactured in Japan today."
"Younjun Soubi"
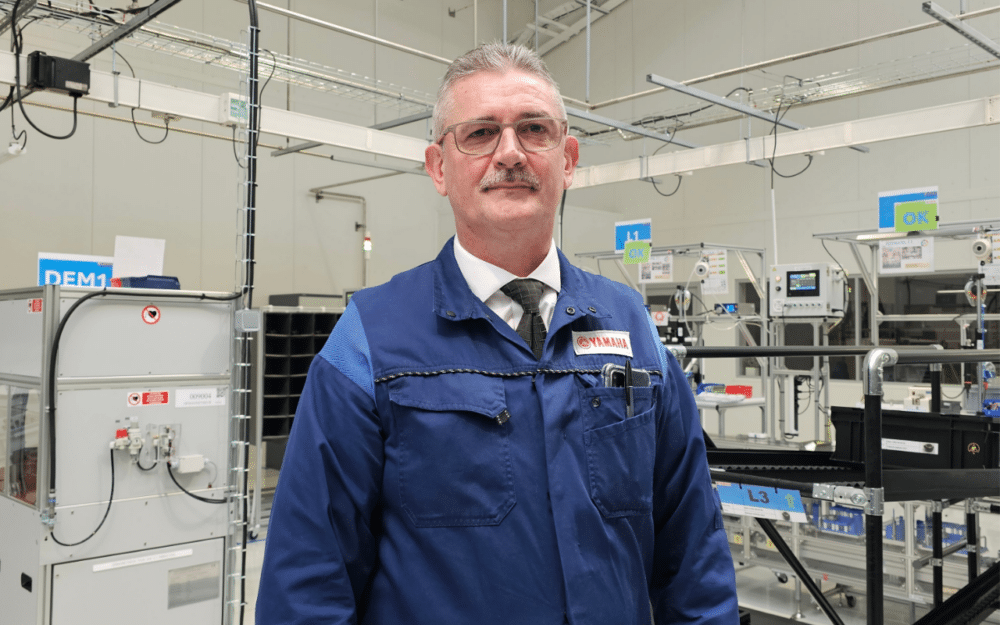
RUSTICI)
The French teams insisted on seeking imperatives of safety and quality as advocated in Japan. For Herve Daty, it is first safety, then quality, and after productivity. And this methodology has a name in Japan, the Younjun Soubi:
"It's a work mentality where operators are put forward. They are the ones who will get involved to achieve the workshop's objectives, especially safety and quality. In the morning before the teams start production, the team checks if the safety devices are functioning correctly, if the operators all have their tools to work, and if all the equipment is properly set up.
Safety is not the same in all companies. We have greatly reinforced the signage in the workshop, safety. Operators, as part of Younjun Soubi, have things to do, to test, and emergency stops to test every morning in turn.
They must check that their machine is operating normally, the safety check, and the process check. They will check different points of the range and the proper functioning of their assembly to achieve 100% quality in their process." Only once all these tests are completed can the line manager give the go-ahead to start production.
Special attention is paid to the health of each operator, especially because the new line is designed for shift work. If the operators do not feel well, we can, for example, transfer them to another less demanding position, explains Herve Daty: "We develop maximum versatility among operators to avoid too much fatigue during the day.
So every two hours or every half day, we change positions. We have more complicated, physically demanding positions than others, so we train them for all positions and we can move them to quieter, less tense positions from time to time. That is also part of the Younjun Soubi."
Carbon Footprint
Yamaha Motor wants to play an active role in the transition to a more sustainable economy to achieve carbon-neutral production by 2035 and meet the Paris Agreement.
Olivier Prevost, the current CEO of Yamaha Motor Europe who succeeded Eric de Seynes, stated: "We are committed to reducing our environmental footprint by adopting more environmentally friendly local production practices and fostering innovation in sustainability." The company plans to install a photovoltaic solar power plant at the Saint-Quentin site within the year.
This plant will generate 10% of the site's electricity needs.
Additionally, the site plans to double shifts and transition to a 2/8 schedule.
References
- ^ inauguration and then visit the new electric bicycle motor assembly plant of the Yamaha Motor Group in France (www.yamaha-motor.eu)
- ^ Yamaha Motor (www.directindustry.com)
- ^ Accell Group (www.accell-group.com)
- ^ Japan. (emag.directindustry.com)